Are balers safe to use?
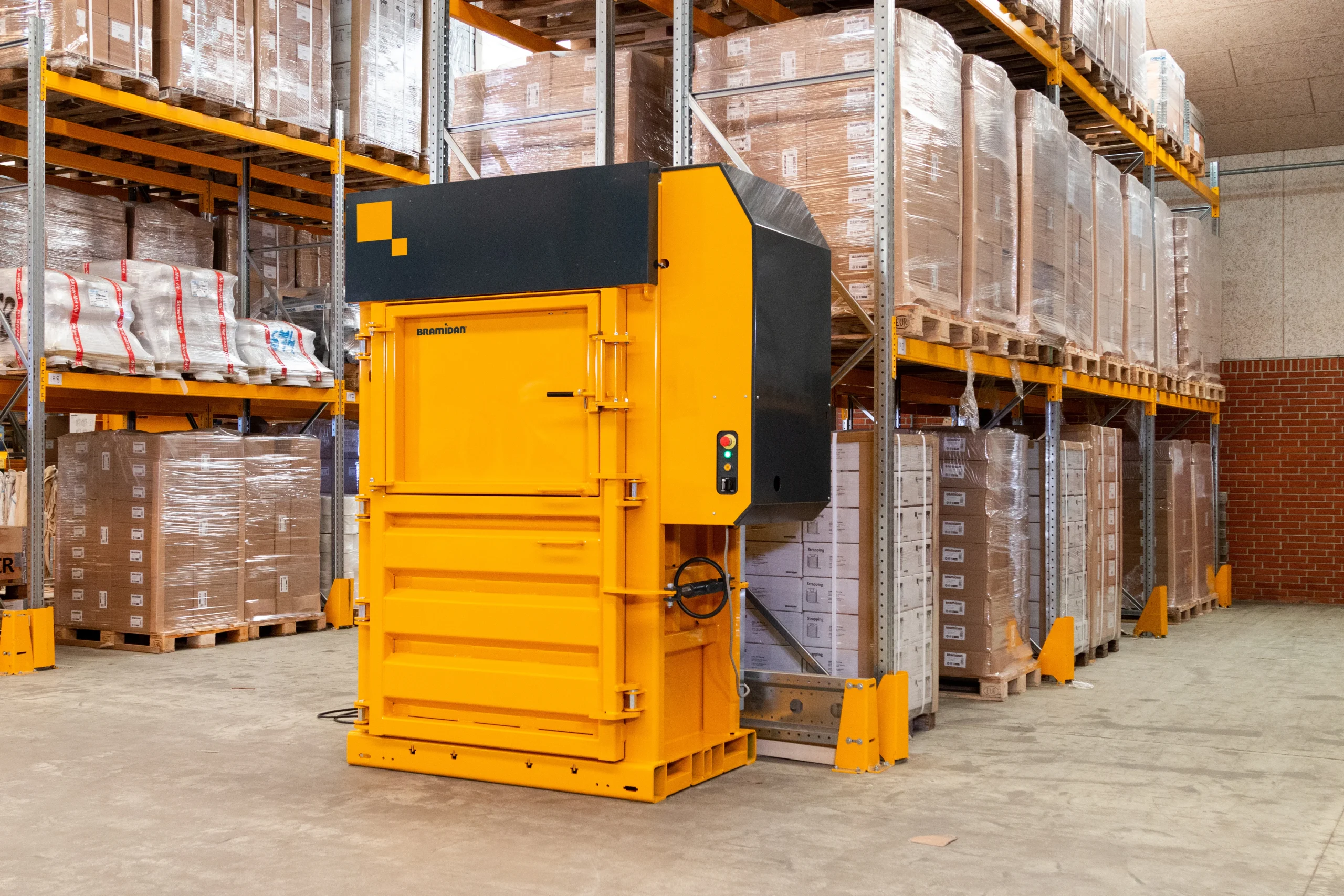
Balers and safety: Debunking the myth
Contrary to popular belief, balers are not a danger to employees. In fact, in our experience in the American and European markets, balers increase safety, organisation, and space optimisation all at once.
Of course, it’s important to invest in a reliable manufacturer and machinery that works best for you, your team, and your space.
At Bramidan, our machinery is designed and manufactured to meet the highest ANSI safety standards. When operating our machines, you can expect ultra-safe operation, without compromising on comfort or efficiency.
We always recommend verifying whether the baler you’re considering, even if it’s not a Bramidan product, has been manufactured in compliance with the latest safety standards. Ensuring the safety of your employees is crucial. But why should you opt for certified machines? Let’s explore safety standards and their significance.
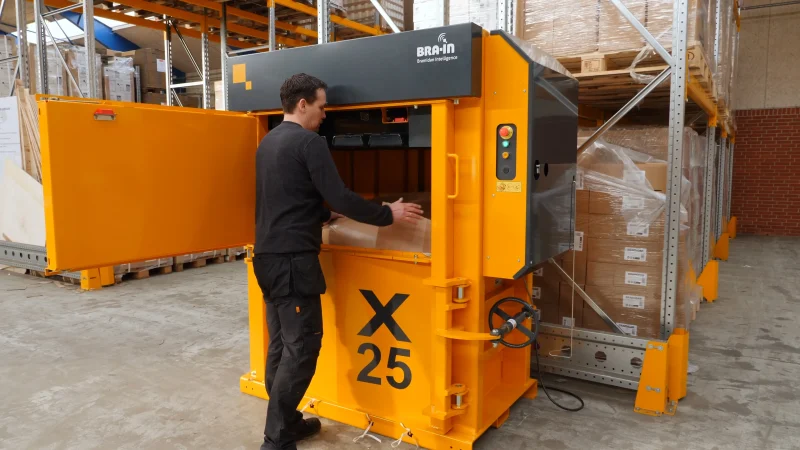
1. Secure operation

2. Redundant safety checks
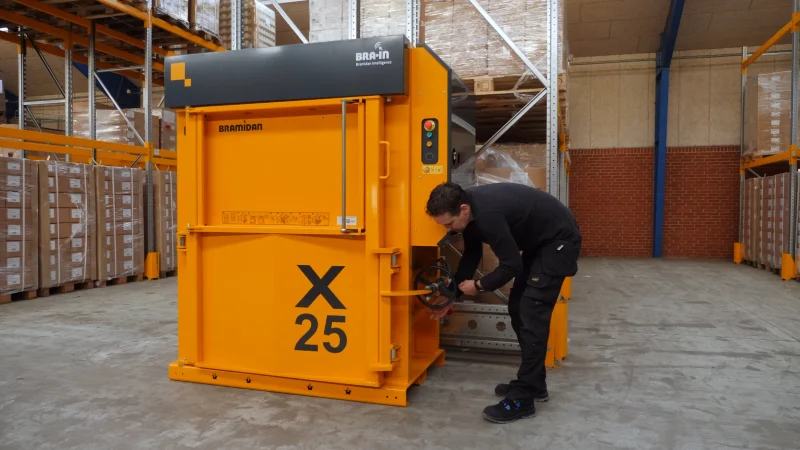
3. Controlled opening with spindle
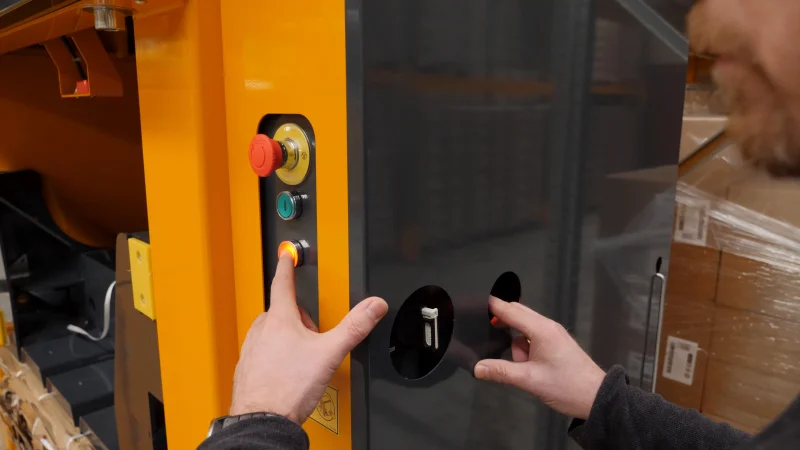
4. Safe bale ejection
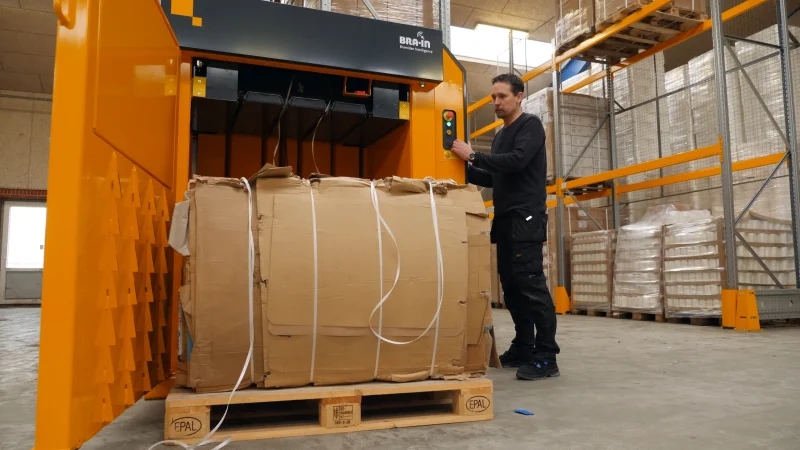
5. Two-button operation for ejection
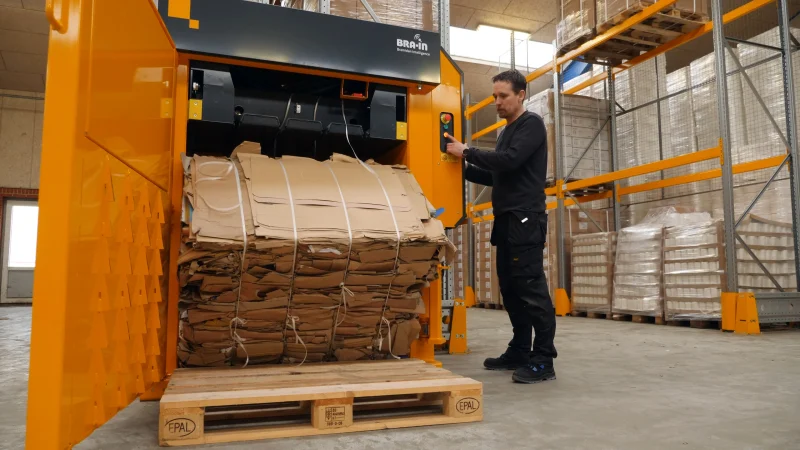
6. Controlled ejection speed
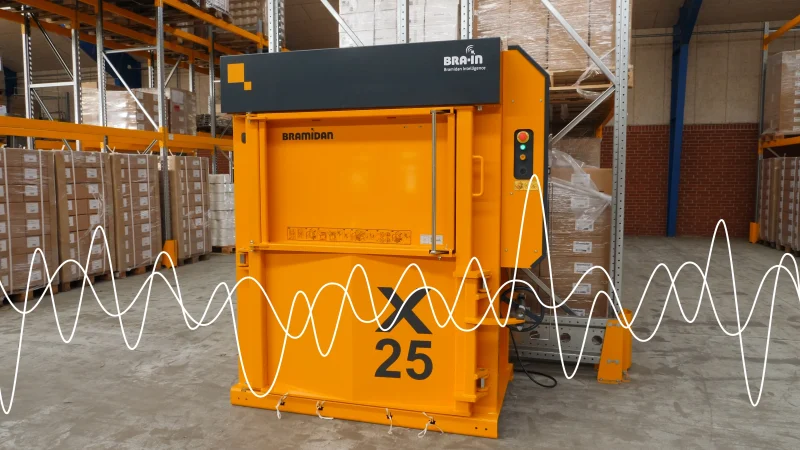
7. Optimised for minimum noise
OSHA safety standards and why they are important
QSHA safety standards protect operators of balers and vertical presses in their workspace. The standards outline design and technical requirements for the baler, providing users with safety checkpoints at every stage of machine operation.
OSHA specifies several areas of attention
The baling chamber, the ejector mechanism, control panels, noise reduction, bale ejection area, emergency stop systems, labels and operating instructions, as well as any potential hazards that could occur to the operator.
Safety focus
Balers made safe by design
When you purchase one of our balers, rest assured that you’re investing in the highest level of safety. Rely on vertical balers that have been crafted with decades of experience.
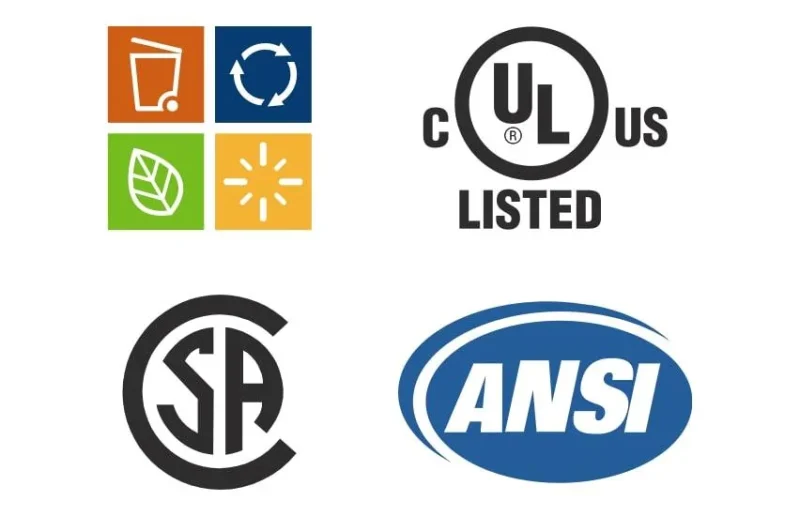
Why choose balers in accordance with ANSI and OSHA standards?
1. Baler will NOT operate if door is open
To reduce the risk of starting the press when the door is open, our line of balers will not operate until the door is fully closed.
In the case of a baler with a manual door like the Flap Door (FD), you can only open the baler door after the end of the waste pressing cycle. If you have a baler with a semi-automatic door (SD), the door automatically closes and opens again when the start button is pushed and the press cycle is completed. If anything hinders the automatic door (i.e. cardboard box or the operator’s hand), the door immediately returns to its fully open position, without doing any harm.
2. Extreme failure prevention
While a door switch plays a crucial role in preventing the machine from operating with the door open, it’s not the sole safeguard in place. In the unlikely event of the door switch malfunctioning, the control unit acts as an additional fault verifier, ensuring that the baler ceases operation and mitigates the risk of any potential injuries.
By implementing this double-check system, the likelihood of the baler press plate being activated during a machine malfunction is significantly reduced.
3. Strong turnbuckle provides full control of door opening
Bramidan balers are equipped with a strong spindle to prevent the door from opening too quickly – which could injure the operator. The threaded turnbuckle maintains steady and full control of the baler door, guaranteeing the operator’s safety when operating the machine, even in limited spaces.
4. Safe ejection of the pressed bale
According to ANSI and OSHA, the speed at which the bale is ejected onto a pallet or floor must be slow and controlled.
Following these guidelines, Bramidan waste balers prevent the bale from turning more than 90 degrees when being ejected from the chamber. Resultingly, the risk of uncontrolled movement of the bale during ejection is extremely low.
5. Very low noise levels during operation
In order to maintain the best possible working environment, our machines generate the one of the lowest possible noise during operation. After all, your workspace deserves a comfortable, low-noise profile, without sacrificing the safety of your team.
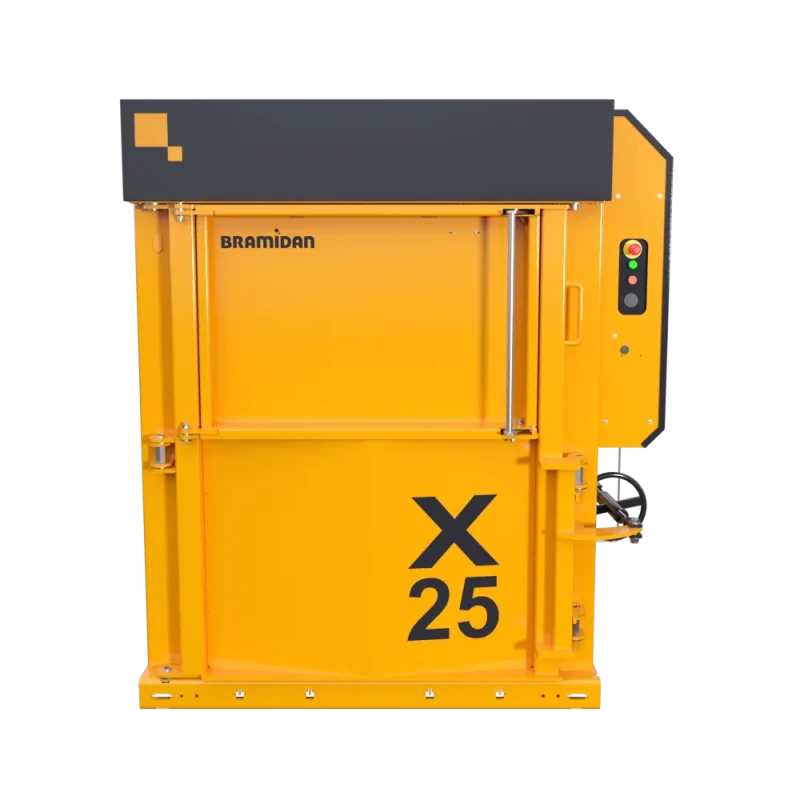
Choose a safe waste baler
- Protection against moving machine parts
- Elimination of electrical hazards
- Minimizing the noise level of the machine working
- Ergonomic design provides the operator with a comfortable working position
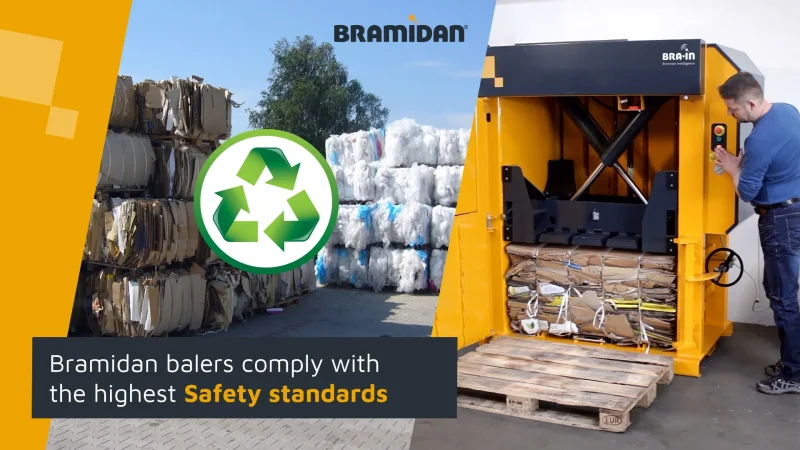
Fill in the form and we will contact you
Questions? Contact us today
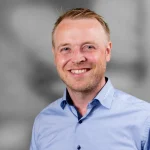
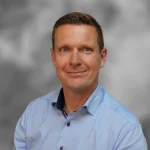
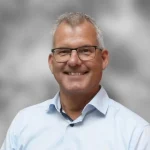
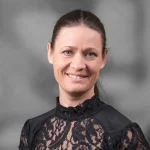
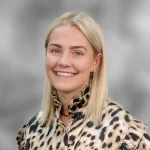
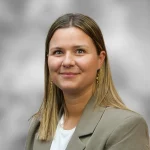